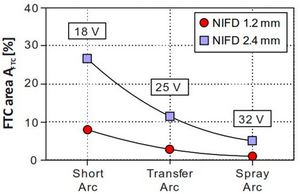
Authors:Frank Schreiber, Benedikt Allebrodt, Tim Erpel
Abstract
The protection of machinery and structural components by thermal coatings is of huge economic importance. Each hour of downtime, caused by deficient coatings as a result of wear and corrosion, costs a fortune. Savings by reducing these downtime hours can be achieved by applying optimized functional coatings which show enhanced properties. The main welding processes for applying coatings are GMAW or OA, PTA or Laser, each with their pros and cons. The PTA process can be seen as the intermediate process bridging the low cost, high deposition rate and the expensive but high end Laser. Recently, the PTA and especially the laser process are gaining more attention and market shares. Nowadays the flux-cored wires can be upgraded more and more with for instance complex carbides and achieve coatings similar to the high performance coatings obtained by PTA and Laser welding but at much lower costs. The common problems accompanying the GMAW process: a large heat affected zone and dilution, can be circumvented by using the cold metal transfer (CMT), the AC-GMAW- and the GMAW hot wire process, allowing the flux-cored wires to fully deploy their large potential and compete with the welding techniques. The current paper will describe the modern GMAW hot wire process and then deal with innovative materials and process concepts for the high performance flux-cored wire to give a competitive alternative for the PTA process and expensive laser.
Key words: Thermal coatings; Flux-cored wire; GMAW-hot wire; Wear; Corrosion; Complex carbides.
DOI: 10.24867/ATM-2018-2-004