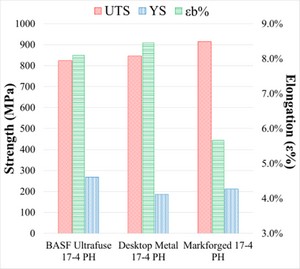
Authors: Luigi Maria Galantucci, Alessandro Pellegrini, Maria Grazia Guerra, Fulvio Lavecchia
Abstract
Additive Manufacturing (AM) is the fabrication of real three-dimensional objects from plastics and metals by adding material, layer by layer. One of the most common AM processes is the Material Extrusion (ME) based on different approaches: plunger, filament and screw. Material Extrusion technologies of metal-polymer composites is expanding and it mainly uses the filament or plunger-based approaches. The feedstock used is a mixture of metal powder (from 55 vol% to about 80 vol%) dispersed in a thermoplastic matrix, as the Metal Injection Molding (MIM) materials. The process consists of three steps: shaping, debinding and sintering. The first step provides the extrusion of filament to realize a primary piece called “green part”; subsequent steps, debinding and sintering, allow to obtain a full metal part by dissolving the polymeric binder. The latter can be carried out using solvents, heat and the combination of them. The interest toward this technology is driven by the possibility to replace other Metal AM technologies, such as Selective Laser Melting or Direct Energy Deposition, in sectors like rapid-tooling or mass production, with several benefits: simplicity, safety to use and saving material and energy. The aim of this keynote is to provide a general overview of the main metal ME technologies considering the more technical aspects such as process methodologies, 3D printing strategy, process parameters, materials and possible applications for the manufacturing of samples on a 3D consumer printer.
Key words:Fused Filament Fabrication, Metal Extrusion, SDS process;
DOI: 10.24867/ATM-2022-1-005