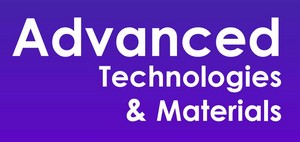
Authors: Srđan Bulatović, Vujadin Aleksić, Bojana Zečević, Biljana Prohaska
Abstract
Designing, constructing and putting into operation a hydroelectric power plant includes complex tasks. Stresses of turbine and hydromechanical equipment of hydro power plants arise during the production of parts and assembly of equipment (residual stresses), in the process of performing functional requirements in exploitation and in the disturbed process of exploitation. After several decades of constant exploitation of the horizontal bulb turbine, which is an integral part of the hydroelectric power unit, empirically, the formation of a crack occurs in the turbine shaft due to the influence of corrosion, erosion and cavitation. Through experimental tests and calculations it has been determined that values of bending stresses of the turbine, which occur due to the action of fatigue and corrosion, as well as stress concentration, are bigger than 25 MPa for flanges exposed to water, and in other case bigger than 40 MPa for flanges exposed to `corrosive water` and can cause the occurrence of surface cracks on the transition radius between the cylindrical part of the shaft and the flange. It has been determined that stress values in the zone under the influence of bending stresses were bigger than allowable values, which led to the occurrence of many cracks due to fatigue corrosion. One of those cracks caused the failure of the shaft and of the whole turbine.
Key words: crack, turbine shaft, fatigue, stress concentration
DOI: 10.24867/ATM-2023-1-004